Российские ученые впервые напечатали на 3D-принтере крупногабаритный корпус вертолетного двигателя
Метка:
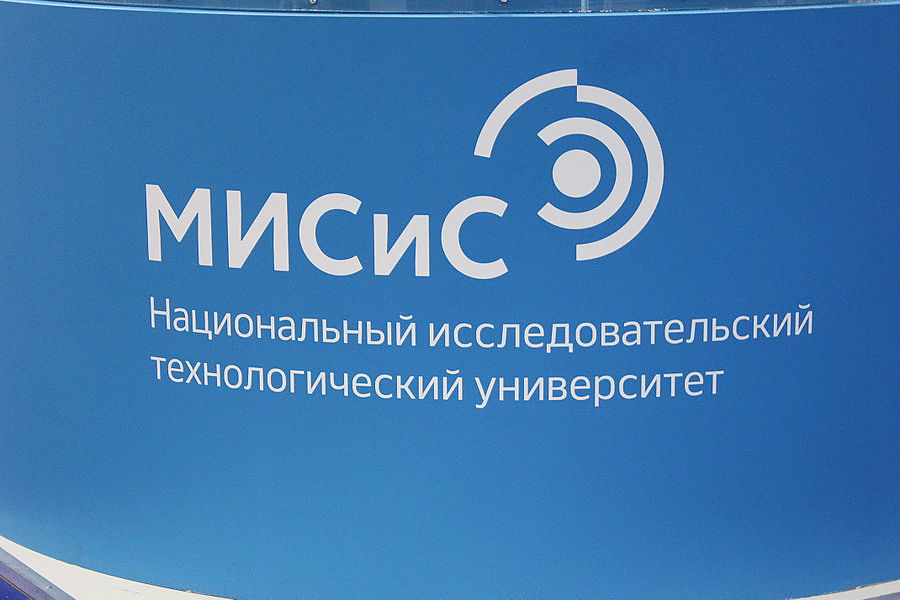
МИСиС
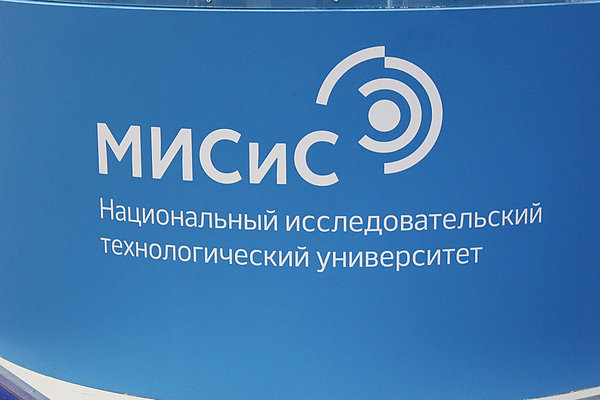
МИСиС
Российские ученые впервые напечатали на 3D принтере крупногабаритный корпус вертолетного двигателя. Об этом сообщает Агентство городских новостей "Москва" со ссылкой на данные национального исследовательского технологического университета "МИСиС".
"Внутренний корпус двигателя российского вертолета ВК-2500, полностью созданный методом послойного лазерного сплавления, представлен на стенде министерства науки и высшего образования РФ на форуме "Открытые инновации" в Сколково. Применение аддитивных технологий для изготовления двигателя позволило сократить срок изготовления до 14 дней. Его разработчиками стали НИТУ "МИСиС" и Санкт-Петербургский государственный морской технический университет (СПбГМТУ)", - говорится в сообщении.
Как отмечается, при создании внутреннего корпуса вертолетного двигателя ВК-2500 была использована аддитивная технология послойного лазерного сплавления – крупная функциональная деталь сложной геометрической формы была полностью "напечатана" из порошка титанового сплава.
"Представленный функциональный узел действительно уникален. Можно с уверенностью сказать, что это первая деталь такой сложности и такого габарита, полученная в России с помощью технологии послойного лазерного сплавления из отечественных порошковых материалов", – заявляет исполнитель проекта, заместитель директора по научной и проектной деятельности института лазерных и сварочных технологий СПбГМТУ Евгений Земляков.
Он добавил, что применение метода послойного лазерного сплавления в сочетании с оптимизацией режимов 3D-принтера кардинально снизило объем последующей механической обработки корпуса двигателя (шлифовки, обтачки, протравки и так далее), соответственно, сократились сроки изготовления – до 14 дней. Это дало возможность снизить производственную себестоимость узла, обеспечивая тем самым общую конкурентоспособность отечественного авиадвигателя.
"Совместно с коллегами из НИТУ "МИСиС" мы реализуем комплексный проект, в котором разрабатываются наиболее интересные с точки зрения промышленного применения аддитивные технологии. Это прямое лазерное выращивание и послойное лазерное сплавление (SLM-технология). У каждой технологии своя область применения. Прямое выращивание используется нами для изготовления заготовок габаритами от 0,5 м до 2 м. Послойный лазерный синтез – для заготовок размером до 0,4 м", - сказал Земляков.
Уточняется, что послойное лазерное сплавление – аддитивная технология, для которой характерны специфические особенности.
"Внутренний корпус двигателя российского вертолета ВК-2500, полностью созданный методом послойного лазерного сплавления, представлен на стенде министерства науки и высшего образования РФ на форуме "Открытые инновации" в Сколково. Применение аддитивных технологий для изготовления двигателя позволило сократить срок изготовления до 14 дней. Его разработчиками стали НИТУ "МИСиС" и Санкт-Петербургский государственный морской технический университет (СПбГМТУ)", - говорится в сообщении.
Как отмечается, при создании внутреннего корпуса вертолетного двигателя ВК-2500 была использована аддитивная технология послойного лазерного сплавления – крупная функциональная деталь сложной геометрической формы была полностью "напечатана" из порошка титанового сплава.
"Представленный функциональный узел действительно уникален. Можно с уверенностью сказать, что это первая деталь такой сложности и такого габарита, полученная в России с помощью технологии послойного лазерного сплавления из отечественных порошковых материалов", – заявляет исполнитель проекта, заместитель директора по научной и проектной деятельности института лазерных и сварочных технологий СПбГМТУ Евгений Земляков.
Он добавил, что применение метода послойного лазерного сплавления в сочетании с оптимизацией режимов 3D-принтера кардинально снизило объем последующей механической обработки корпуса двигателя (шлифовки, обтачки, протравки и так далее), соответственно, сократились сроки изготовления – до 14 дней. Это дало возможность снизить производственную себестоимость узла, обеспечивая тем самым общую конкурентоспособность отечественного авиадвигателя.
"Совместно с коллегами из НИТУ "МИСиС" мы реализуем комплексный проект, в котором разрабатываются наиболее интересные с точки зрения промышленного применения аддитивные технологии. Это прямое лазерное выращивание и послойное лазерное сплавление (SLM-технология). У каждой технологии своя область применения. Прямое выращивание используется нами для изготовления заготовок габаритами от 0,5 м до 2 м. Послойный лазерный синтез – для заготовок размером до 0,4 м", - сказал Земляков.
Уточняется, что послойное лазерное сплавление – аддитивная технология, для которой характерны специфические особенности.
